“공장이 아니라 완전 캠퍼스네…”
연구원・연구소에 극장과 카페・스크린골프장・농구장에 헬스장까지
티센크루프 엘리베이터 코리아(대표 박양춘)의 천안공장은 국내 승강기업계에서 유일하게 ‘스마트팩토리’를 구현한 곳이다. 하지만 티센크루프맨들은 이곳을 공장이 아닌 캠퍼스라 부른다. 연구와 제조, 문화, 스포츠공간이 한 데 어우러져 있어 마치 대학캠퍼스를 방불케 하기 때문이다. 승강기를 제조하는 생산시설에 연수원과 연구소가 들어섰고, 직원복지를 위한 극장, 갤러리, 카페 등을 비롯해 스크린골프장, 농구장, 족구장, 배구장, 사우나, 헬스장 등 없는 게 없다. 천안캠퍼스가 기존의 일반적인 스마트공장과 차별화되는 요소다.
◆자동화 판금설비·로봇용접기 도입…생산성 30% 향상
안성휴게소에서 하행 경부고속도로를 타고 15분쯤 가다보면 왼쪽에 높게 솟은 승강기타워를 볼 수 있다. 타워 옆에는 축구장 5개를 합쳐 놓은 크기(3만6000㎡)의 공장이 있다. 200억원이 들어간 천안캠퍼스는 자동화설비는 물론 사물인터넷과 빅데이터를 활용해 ‘똑똑한 생산시설’로 거듭났다.
이 회사는 승강기 업계 최초로 자동화 판금설비를 도입했다. 여러 사람이 하는 일을 기계가 대신해 제품 품질에 대한 신뢰성을 확보하고, 친환경 공정을 구축한 것이다. 이는 생산성과 효율성을 개선하기 위한 작업이다. 더욱이 똑똑한 제조업을 표방하는 4차 산업혁명 시대를 위한 포석이기도 하다.
가장 큰 변화는 생산라인의 인력감소다. 자동화 판금설비가 설치되면서 13명이 하던 일을 이제는 4명만 있어도 가능해진 것이다. 기존에 승강기 판넬을 잘라내고, 구부리고, 철판에 구멍을 내고, 용접하는 각각의 공정은 작업자가 일일이 기계를 조작해야 했다.
하지만 자동화 판금설비가 구축돼 이 모든 공정이 버튼 하나로 한 번에 가능해졌다. 설비를 조작하고 판넬을 나르는 시간이 줄어들어 더욱 빠른 시간에 더 많은 승강기 제작이 가능해졌다.
윤영섭 티센크루프 스마트팩토리추진실장은 “도어 하나를 만드는데 기존에는 89초 걸리던 것이 이제는 76초로 줄어 생산속도가 17% 향상됐다”며 “콘트롤러 역시 기존 150분에서 123.7분으로 21% 개선됐다”고 말했다.
또 로봇용접기를 두 대나 설치해 공정시간을 한층 단축했다. 다른 제조 산업에선 흔히 볼 수 있는 로봇이지만 승강기 기업에선 최초로 도입됐다. 1mm 오차도 허용하지 않는 로봇으로 정교함을 구현하고, 효율성을 높였다. 불꽃이 튀는 위험한 일을 로봇이 대신하니 작업자의 안전도 더욱 강화됐다.
판금생산라인에서 인력이 3분의 1 줄었지만 생산성은 30% 이상 개선됐다. 생산규모도 기존 연간 1만대에서 2만대로 2배나 늘었다. 그렇다고 고용 인력을 줄인 것은 아니다. 오히려 남은 9명을 인력이 부족한 다른 현장에 투입해 단점을 보완했다.
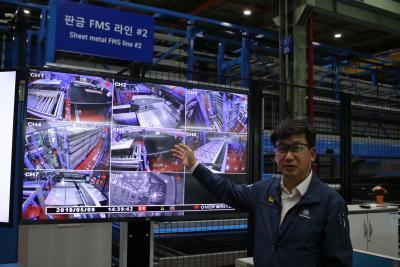
◆스마트품질보증시스템 적용…불량률 30% 낮춰
티센크루프는 2014년부터 스마트팩토리를 구축하기 시작했다. 그룹본사 차원에서 제조혁신의 표본으로 일컬어지는 일본의 도요타자동차 생산방식을 차용해 전 세계 10개 공장에 도입한 것이 계기가 됐다. 한국법인인 티센크루프 코리아도 이 방식을 적용했지만 여기서 머무르지 않고 IT강국의 장점을 살려 스마트팩토리를 추진한 것이다.
윤 실장은 “당시 ‘작지만 강하고, 똑똑한 공장 만들자’라는 슬로건으로 3단계 스마트팩토리 구축 로드맵을 세웠고, 이는 전 세계 티센크루프 공장 10개 중 유일하게 진행하고 있다”며 “2014년부터 2017년까지 1단계 사업이 마무리됐고, 현재는 2단계 사업(2018년~2019년)이 한창”이라고 말했다.
1단계 사업은 공장에 도요타생산방식을 입힌 뒤 IoT와 빅데이터 등을 활용해 스마트자재고관리, 스마트 설비관리, 공정검사, 작업방식, 스마트 물류 등을 적용했다. 그러다 2017년에는 아예 스마트팩토리추진실을 신설해 본격적인 2단계 사업을 진행했다.
2018년 시작된 2단계 사업은 생산정보화(MIS; Manufacturing Information System)에 초점이 맞춰져 있다. 재고를 최소한으로 줄여 비용을 줄이고, 고객주문에 선제적으로 대응할 수 있는 시스템을 갖추는 것이다. 2단계의 핵심은 적기 생산, 적기 출하다.
여기에 스마트품질보증시스템을 적용해 불량률을 30%나 낮췄다. 천안캠퍼스에는 생산된 승강기의 품질을 확보하기 위해 ▲품질인증팀(QE) ▲품질보증팀(QA) ▲품질관리팀(QC)을 운영하고 있다.
전 세계 10개 공장에서 다루는 부품의 가격과 품질, 협력사의 경영상태, 제조수준 등에 대한 정보를 서로 공유함으로써 더욱 뛰어난 품질관리가 이뤄지는 것도 장점으로 통한다.
또 생산라인에 이어 사무공간에서도 시간을 줄이는 일은 계속된다. 비효율적인 절차 등을 간소화해 능률적인 업무가 가능하도록 관련 툴을 개발해 적용하고 있다. 현재 27개 중 10를 개발해 현장에서 사용하고 있다.
윤 실장은 “스마트팩토리추진실은 그동안 따로 떨어져 있던 데이터를 한 곳에 모아 누구나 쉽게 관련 정보에 접근하고, 공유할 수 있는 프로그램을 만들어 업무시간 줄이기에 앞장서고 있다”며 “공장 및 사무자동화로 인해 천안캠퍼스에는 야근이 없고, 주40시간 일하는 공간으로 탈바꿈했다”고 말했다.
이어 “과거보다 더 적은 시간을 일하지만 생산성을 개선되고, 직원들의 만족도도 훨씬 높다”며 “천안캠퍼스는 ‘저녁이 있는 삶’이 보장되는 스마트팩토리”라고 덧붙였다.
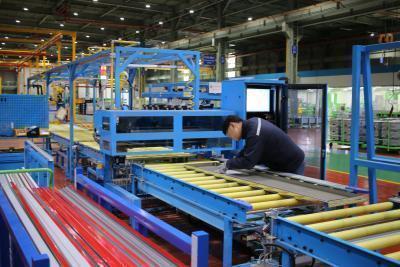
◆적기생산·적기조달 모토로 최적화된 재고관리…효율성
생산라인에서 만들어진 승강기 부품들이 마지막으로 향하는 곳이 바로 물류창고다. 8400㎡ 면적의 물류센터에는 출하를 기다리는 수많은 부품이 빼곡히 쌓여 있었다.
반자동 컨베이어시스템과 바코드시스템을 구축해 어떤 부품이 언제, 누구에게, 얼마만큼 배송되는지를 실시간으로 확인할 수 있다. 이 모든 출하정보를 작업자가 수동으로 확인하지 않고, 태블릿PC 한 대로 언제 어디서나 알 수 있다. 뿐만 아니라 이러한 정보는 SNS를 통해 고객에게도 전달된다.
또 ERP 전산시스템을 도입해 모든 부품에 대한 재고관리가 가능해진 점도 가장 큰 변화다. 제품에 대한 판매정보가 쌓여 빅데이터를 형성, 이러한 데이터 분석을 통해 연간 생산량을 계획하고 일정을 조절할 수 있다. 빅데이터를 활용해 신제품 개발에도 나설 수 있다.
빅데이터, IoT(사물인터넷) 등 소프트웨어와 결합한 하드웨어(생산라인)로 ‘똑똑한 공장’을 구현한 것이다.
엘리베이터는 산업특성상 생산 공장에서 부품을 만들어 이를 현장에 운반해 조립하는 방식이다. 때문에 스마트물류시스템은 적기조달을 위해 반드시 필요하다. 엘리베이터 부품세트가 만들어지면 공장에서 연결된 물류센터로 보내져 현장별로 분류된다. 배송담당자는 센터내 모니터를 통해 자신이 운반해야할 엘리베이터를 확인해 제품을 차량에 싣는다. 이러한 모든 과정에 대한 정보는 현장의 설치팀에도 전해져 누구라도 실시간으로 제품의 생산·재고·운반 상태를 알 수 있게 된다.
윤 실장은 “2020년 모든 공정이 마무리되면 천안캠퍼스는 전 세계 티센크루프 공장의 모범이자 리더 역할을 할 수 있을 것”이라며 “4차 산업혁명 시대에 티센크루프는 전세계 승강기 산업의 롤모델이 될 수 있기를 기대한다”고 말했다.